I’m working on this little 17′ roto molded beach trimaran. It is intended for resorts.
Alii Nui on Maui
I had not yet seen the updated website for the 65′ , 100 passenger Alii Nui. This KHSD charter cat was built in foam/glass by Schooner Creek.
See http://www.aliinuimaui.com/maui-sailing.htm
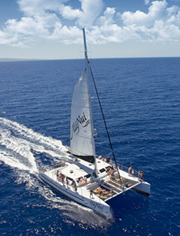
Visitors Today
Gone Next Week
I will be out of the office Feb. 19 through 26. I might not even have email.
More Keeping My Head Down
New Record
Congratulations. The guys and a girl, Team Hallin, the trimaran rowing team using KHSD hull lines just arrived in Barbados to set a new world record across the Atlantic. See the arrival webcam at http://www.portstcharles.com/webcam_window.php?cam=3.
And http://www.teamhallin.co.uk/wp/ for the announcement.
I’ve had my head down..
Daycharter in the Cold
I had forgotten there was a brave daycharter company operating right up in Blaine, Washington. They use one of my 36′ charter boats in a box. Bring your warm coat. See http://rapscallionsailcharters.com/index.html
Atlantic Rowing update
Team Hallin, with KHSD hull design, is half way across the Atlantic. It is still leading the rowing race and is still on track for a new record. See the chart at http://www.oceanrowing.com/SaraG_2011_comparative.htm and articles on the race at http://www.teamhallin.co.uk/wp/
African Catamaran Ferry Project Update
The KHSD designed 65′ catamaran for Lake Victoria is looking better than I have seen it look yet. I’m still worried about the weight. See also http://www.earthwiseventures.com/The_Ferry_Project.html
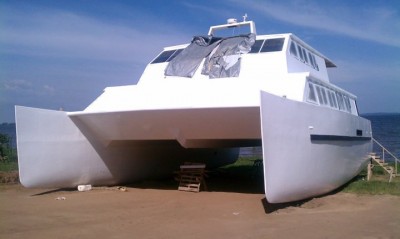